Nonwoven fabrics, a mid-20th-century innovation, have transformed the textile industry with their unique production methods and versatile applications. Unlike traditional woven or knitted textiles, nonwovens are created through processes that bond or entangle fibers, offering a range of benefits from cost-efficiency to customizable properties.
These fabrics can be tailored to meet specific needs, from lightweight and breathable to heavy-duty and waterproof, making them suitable for applications in healthcare, hygiene products, filtration systems, and more. The use of synthetic and natural fibers in their production allows for a sustainable approach to textile manufacturing.
This guide offers an in-depth look at nonwoven fabrics, exploring their types, properties, applications, and the innovative potential that positions them at the forefront of modern textile technology.
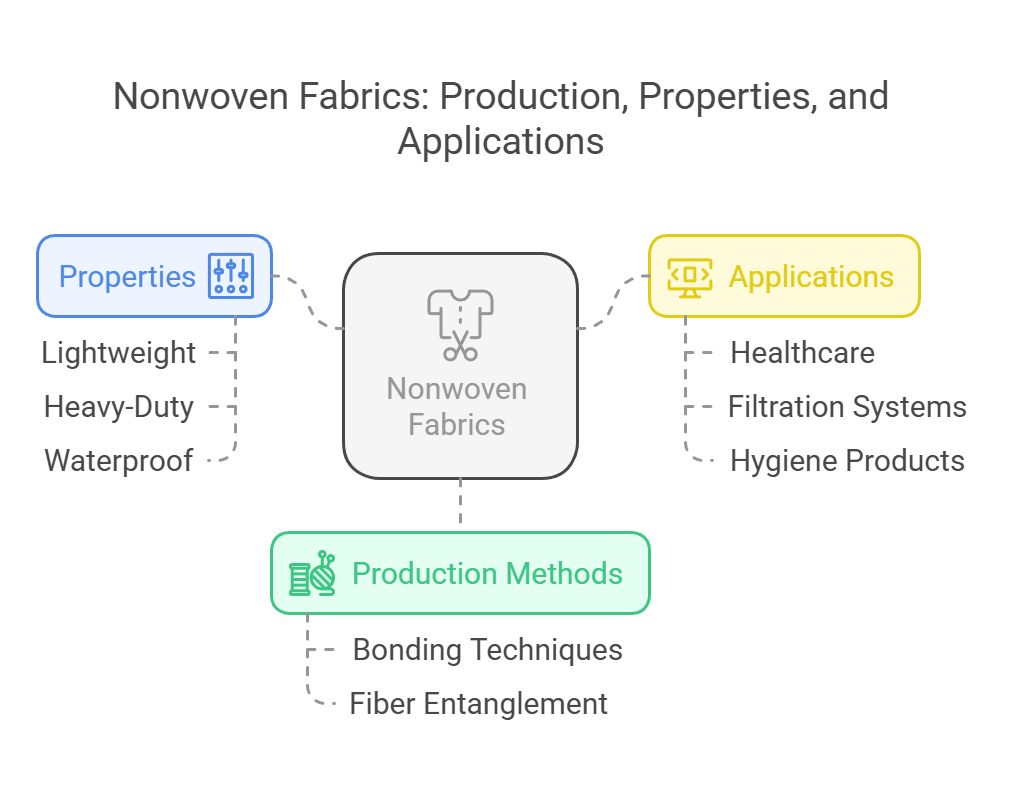
Understanding Nonwoven Fabric: Definition, Properties, and Applications
Nonwoven fabrics have become a significant part of the textile industry, offering a range of applications and advantages that set them apart from traditional woven and knitted fabrics. The concept of nonwoven fabrics dates back to the mid-20th century, when technological advancements allowed for the development of new materials that did not require the conventional weaving or knitting processes. The unique structure and production methods of nonwoven fabrics have since revolutionized many industries, from medical to automotive.

Unlike woven fabrics, which are created by interlacing yarns in a crisscross pattern, or knitted fabrics, which are made by interlocking loops of yarn, nonwoven fabrics are produced by bonding or entangling fibers together. This can be achieved through various methods such as mechanical, thermal, or chemical processes. The result is a fabric that is not only versatile but also efficient in terms of production and cost.
One of the key characteristics of nonwoven fabrics is their diverse range of properties, which can be tailored to meet specific requirements. For example, they can be engineered to be lightweight or heavy, breathable or impermeable, and soft or stiff. This adaptability makes nonwoven fabrics suitable for a wide array of applications, including hygiene products, medical supplies, filtration systems, and geotextiles.
The production of nonwoven fabrics typically involves the use of synthetic fibers like polypropylene, polyester, and nylon, although natural fibers such as cotton and wool can also be used. The choice of fibers and production method depends on the intended use of the fabric. For instance, spunbonding and meltblowing are common techniques for creating nonwoven fabrics with specific properties that are ideal for disposable products and industrial applications.
In summary, nonwoven fabrics represent a significant advancement in textile technology, offering unique structural and functional benefits that distinguish them from traditional fabrics. Their innovative production methods and versatile properties continue to drive their popularity across various sectors, making them an essential component in modern manufacturing and product development.
What is Nonwoven Fabric?
Nonwoven fabric is a versatile material characterized by its unique production technique, which does not require weaving or knitting. Instead, it is produced directly from fibers, which are bonded together through various methods. The composition of nonwoven fabric can vary widely, utilizing natural fibers like cotton and wool, synthetic fibers such as polyester and polypropylene, or blends of these materials. This diversity in fiber selection allows nonwoven fabrics to be tailored for specific applications based on desired properties such as strength, flexibility, and absorbency.

The manufacturing of nonwoven fabric involves several key processes. One common method is bonding, where fibers are adhered together using heat, chemical agents, or mechanical pressure. Another technique is entanglement, which includes processes like needle punching, wherein barbed needles physically intertwine the fibers to create a cohesive fabric. Additionally, chemical methods, such as the application of adhesives or solvents, can be employed to bond fibers together.
Each of these processes results in a different type of nonwoven fabric, each with specific properties suitable for various applications. For instance, spunbond nonwovens are created by extruding filaments and bonding them thermally, producing a strong and durable fabric ideal for applications like geotextiles and agricultural coverings. Conversely, meltblown nonwovens, which are produced by blowing molten polymer through fine nozzles, yield a finer and softer fabric often used in filtration and medical products.
The ability to customize the composition and manufacturing process of nonwoven fabrics makes them highly adaptable to a wide range of industrial, medical, and consumer applications. This adaptability, combined with the efficiency of production, positions nonwoven fabrics as a crucial material in modern manufacturing and product development.
Types of Nonwoven Fabrics
Nonwoven fabrics are categorized by their production methods, each yielding materials with distinct characteristics and applications. Understanding these types is crucial for selecting the appropriate nonwoven fabric for specific purposes.
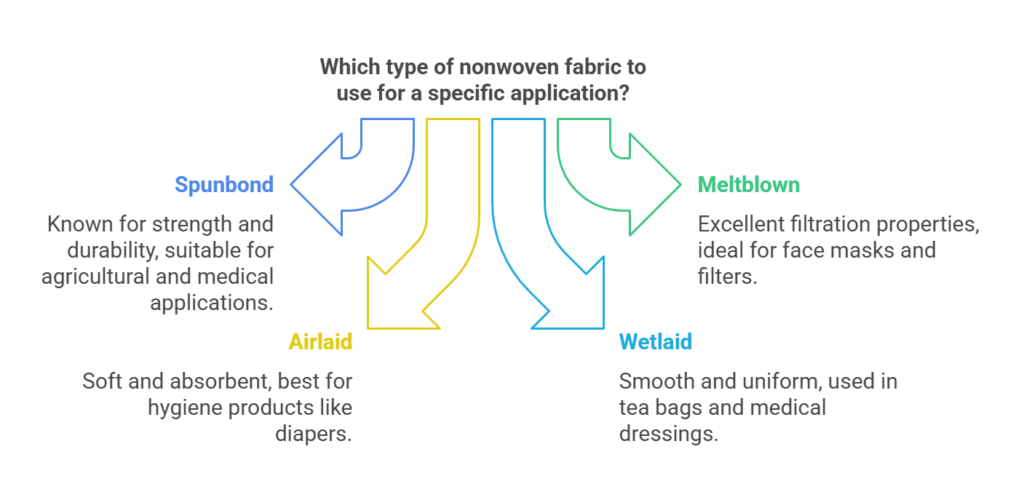
Spunbond nonwoven fabrics are created by extruding thermoplastic polymers into fine filaments, which are then laid randomly on a conveyor belt and bonded together. These fabrics are known for their strength, durability, and cost-effectiveness, making them suitable for applications such as agricultural covers, disposable medical garments, and geotextiles.
Meltblown nonwoven fabrics are produced by extruding molten polymer through small nozzles, using high-speed blowing gas to form fine fibers. These fibers are collected on a conveyor belt and bonded to create a fabric. The resultant material is characterized by its fine fiber diameter, high surface area, and excellent filtration properties. Meltblown nonwovens are primarily used in filtration media, including face masks, air filters, and liquid filters.
Airlaid nonwoven fabrics are made by dispersing fibers into an air stream, which then deposits them randomly onto a moving screen. The fibers are bonded chemically, thermally, or through mechanical entanglement. Airlaid fabrics are known for their softness, absorbency, and bulkiness. They are widely used in hygiene products, such as diapers and sanitary napkins, as well as in wipes and tabletop products.
Wetlaid nonwoven fabrics are formed by dispersing short fibers in water to create a slurry, which is then deposited on a moving screen to form a web. The fibers are bonded through various methods such as chemical bonding or thermal bonding. Wetlaid nonwovens are valued for their smooth surface and uniformity. They are employed in applications like tea bags, medical dressings, and wallpaper.
Each type of nonwoven fabric offers unique properties tailored to specific applications, highlighting the versatility and importance of these materials in diverse industries. Understanding these types is essential for leveraging the strengths of nonwoven fabrics in various practical applications.
Properties of Nonwoven Fabrics
Nonwoven fabrics exhibit a unique set of properties that make them highly versatile for various applications. One of the most significant attributes of nonwoven fabrics is their strength. These fabrics can be engineered to provide different levels of tensile strength, making them suitable for both lightweight and heavy-duty applications. The technique used in their manufacturing, such as spunbonding or meltblowing, significantly impacts their strength characteristics.

Durability is another critical property of nonwoven fabrics. These fabrics can withstand wear and tear, making them ideal for products that require a longer lifespan, such as reusable shopping bags, automotive interiors, and geotextiles. The durability of nonwoven fabrics can be enhanced by incorporating certain additives or by using specific bonding methods like thermal or chemical bonding.
Absorbency is a key property for nonwoven fabrics used in medical and hygiene products. These fabrics can be designed to have high absorbency rates, suitable for applications such as diapers, sanitary napkins, and medical dressings. The absorbency levels can be adjusted by altering the fiber composition or by applying special surface treatments.
Filtration efficiency is another paramount property, particularly for nonwoven fabrics used in air and liquid filtration systems. The microstructure of nonwoven fabrics allows them to trap particles effectively, making them ideal for face masks, HEPA filters, and water purification systems. The efficiency of filtration can be modified by adjusting the fiber diameter, pore size, and overall fabric density.
Additionally, nonwoven fabrics possess other notable properties such as softness, breathability, and flexibility. These characteristics make them suitable for applications ranging from apparel and furnishings to industrial and construction materials. Different manufacturing techniques, such as needle punching, hydroentangling, or chemical bonding, can be employed to tailor these properties to meet specific requirements.
In conclusion, the properties of nonwoven fabrics are highly adaptable and can be customized through various manufacturing processes. This adaptability makes nonwoven fabrics an essential material in numerous industries, providing solutions that meet diverse performance and functional needs.
Nonwoven fabrics are created through a variety of production methods, each with its unique characteristics and applications. Among the primary techniques are dry-laid, wet-laid, and spunmelt processes. These methods involve different machinery and technologies, contributing to the versatility and functionality of nonwoven materials.
Dry-Laid Processes
The dry-laid method involves forming a web of fibers using air or carding devices. Carding machines align fibers in parallel, creating a uniform web. This process can produce lightweight, high-loft fabrics ideal for applications such as insulation, filtration, and cushioning materials. The air-laid technique disperses fibers in an air stream, then deposits them onto a moving belt to form a web, which is subsequently bonded using thermal, chemical, or mechanical means. The versatility of dry-laid processes allows for the production of fabrics with various thicknesses and densities.
Wet-Laid Processes
In wet-laid processes, fibers are suspended in a water-based slurry and deposited onto a forming screen. The water is drained away, leaving a web of interlocked fibers. This method is similar to paper-making and is particularly effective for creating fabrics with high uniformity and strength. Wet-laid nonwoven fabrics are commonly used in applications such as medical disposables, wipes, and filtration media. The ability to incorporate a wide range of fiber types, including natural, synthetic, and recycled fibers, enhances the sustainability and functionality of wet-laid fabrics.
Spunmelt Processes
Spunmelt technologies, including spunbond and meltblown processes, involve extruding molten polymer through spinnerets to create continuous filaments. In the spunbond process, the filaments are cooled and directly deposited onto a conveyor belt, forming a web that is bonded through thermal or mechanical means. Spunbond fabrics are known for their strength and durability, making them suitable for applications such as geotextiles, agricultural coverings, and industrial wipes. Meltblown processes, on the other hand, produce fine, microfibrous webs with excellent filtration properties, ideal for medical masks, air filters, and absorbent materials.
Each production method for nonwoven fabrics has its advantages and specific applications, driven by the machinery and technologies involved. Additionally, the environmental impact and sustainability of these processes are crucial considerations. Innovations in recycling and energy-efficient technologies are being developed to reduce waste and minimize the carbon footprint of nonwoven fabric production. By understanding these various production methods, industries can better leverage nonwoven fabrics for diverse and sustainable applications.
Applications of Nonwoven Fabrics
Nonwoven fabrics have become indispensable across a myriad of industries due to their versatility, cost-effectiveness, and unique properties. One of the most prominent sectors utilizing nonwoven materials is the medical and healthcare industry. Here, nonwoven fabrics are integral in the production of surgical masks, gowns, drapes, and other essential protective gear. Their ability to provide barrier protection while maintaining breathability makes them ideal for preventing infection and ensuring the safety of both patients and healthcare professionals.

In the realm of hygiene products, nonwoven fabrics are extensively used due to their softness, absorbency, and skin-friendly nature. Diapers, sanitary napkins, and incontinence products are prime examples where nonwoven materials provide comfort and functionality. Their high absorbency and ability to wick moisture away from the skin help in maintaining hygiene and preventing irritation.
The automotive industry also benefits significantly from the use of nonwoven fabrics. These materials are employed in various components such as filters, insulation, and interior linings. Nonwoven fabrics used in automotive filters help in maintaining air quality by trapping dust and pollutants, ensuring a clean and safe environment inside the vehicle. Additionally, their insulating properties contribute to noise reduction and temperature control, enhancing overall passenger comfort.
In the construction sector, nonwoven fabrics find applications as geotextiles, which are used for soil stabilization, erosion control, and drainage management. Geotextiles made from nonwoven materials offer durability and resistance to environmental stressors, making them suitable for a wide range of construction and civil engineering projects. Their use in road construction, landfills, and sports field construction underscores their importance in modern infrastructure development.
Overall, the diverse applications of nonwoven fabrics underscore their indispensability across various industries. Their unique properties and adaptability ensure that they will continue to play a crucial role in advancing technology and improving the quality of products and services in the future.
Advantages and Disadvantages of Nonwoven Fabrics
Nonwoven fabrics offer a range of advantages that make them highly appealing in various industries. One of the foremost benefits is their cost-effectiveness. The production process for nonwoven fabrics is generally less labor-intensive and faster compared to traditional woven materials, which translates into lower manufacturing costs. This economic efficiency makes nonwoven fabrics ideal for single-use products such as medical disposables, filters, and hygiene items.

Another significant advantage of nonwoven fabrics is their versatility. These fabrics can be engineered to possess specific properties such as absorbency, resilience, softness, and strength, which can be tailored to meet the needs of diverse applications. For instance, nonwoven materials are extensively used in automotive interiors, geotextiles, and home furnishing products due to their customizable nature. Furthermore, the ease of production allows for rapid scalability, accommodating high-volume demands without compromising quality.
However, nonwoven fabrics also have several disadvantages that must be taken into consideration. One of the primary drawbacks is their limited durability. Unlike woven fabrics, nonwoven materials tend to have a shorter lifespan, especially when subjected to repeated stress or abrasion. This can limit their use in applications where long-term durability is crucial.
Environmental concerns also pose a significant challenge for nonwoven fabrics. Many nonwoven materials are derived from synthetic polymers such as polypropylene, which are not biodegradable. The disposal of nonwoven products, particularly single-use items, can contribute to environmental pollution and waste management issues. Efforts are being made to develop eco-friendly alternatives and recycling methods, but these solutions are not yet universally implemented.
In summary, while nonwoven fabrics offer notable advantages in terms of cost, versatility, and ease of production, they also present challenges related to durability and environmental impact. Balancing these pros and cons is essential for informed decision-making in their application.
Future Trends and Innovations in Nonwoven Fabrics
As the world continues to evolve, nonwoven fabrics are at the forefront of technological and material innovations. Ongoing research and development are driving significant advancements in this sector, paving the way for new materials and enhanced production techniques. One of the most promising areas of development is the integration of biodegradable and renewable raw materials. Scientists are exploring the use of natural fibers, such as bamboo and hemp, which offer sustainable alternatives to traditional synthetic fibers.
Another key area of innovation is the development of smart textiles. These advanced nonwoven fabrics are embedded with sensors and electronic components, enabling them to interact with the environment and the wearer. Applications of smart textiles include healthcare monitoring, where fabrics can track vital signs, and in sportswear, providing real-time performance analytics. The advent of such smart textiles is poised to revolutionize various industries, offering unprecedented functionality and convenience.
The role of nonwoven fabrics in sustainability cannot be understated. With increasing environmental awareness, the demand for eco-friendly materials is on the rise. Nonwoven fabrics are being engineered to be more recyclable and less reliant on petrochemicals. Innovations in chemical treatments and fiber engineering are enhancing the lifecycle of these fabrics, ensuring they meet stringent environmental standards. The push towards a circular economy is fostering the development of nonwoven products that are not only durable but also minimize waste at the end of their lifecycle.
Emerging applications of nonwoven fabrics are also noteworthy. In addition to traditional uses in hygiene products, medical supplies, and filtration systems, nonwoven fabrics are finding new applications in automotive interiors, construction, and agricultural sectors. These materials offer unique properties such as lightweight, strength, and versatility, making them suitable for a wide range of innovative applications.
Overall, the future of nonwoven fabrics is bright, marked by continuous innovation and expanding applications. As research and development efforts intensify, nonwoven fabrics are set to play a crucial role in various industries, driving both functional and sustainable advancements.
2 Responses
Nonwoven fabrics are at the cutting edge of material innovation, blending sustainability with advanced functionality to address modern needs. The exploration of biodegradable and renewable raw materials like bamboo and hemp underscores the shift toward eco-conscious manufacturing, offering sustainable alternatives to synthetic fibers. Meanwhile, the emergence of smart textiles, embedded with sensors and electronics, is revolutionizing industries by enabling fabrics to monitor health, enhance sports performance, and interact with users in real time. These advancements align with the global push for a circular economy, as nonwoven fabrics are being engineered for recyclability and reduced environmental impact. By balancing durability with eco-friendliness, nonwoven technologies are setting a new standard for innovative, sustainable solutions across diverse applications.
hello